Efficient order fulfillment is a critical aspect of running a successful business. In today’s fast-paced e-commerce landscape, customers expect quick and accurate delivery of their orders. Order cycle time is a key metric that measures the time it takes for an order to move through the entire fulfillment process, from placement to delivery. In this article, we will explore what order cycle time entails, discuss strategies to improve it, and shed light on what buyers value the most in terms of order fulfillment.
Understanding Order Cycle Time
Order cycle time encompasses all the activities involved in fulfilling an order, including order processing, picking, packing, and shipping. It begins when a customer places an order and ends when the order reaches the customer’s doorstep. Measuring order cycle time helps businesses identify bottlenecks in their fulfillment process and make necessary improvements to meet customer expectations.
The Importance of Improving Order Cycle Time
E-commerce businesses should strive to offer various shipping options that balance delivery time and cost.
Customer Satisfaction: In the age of instant gratification, customers expect fast and reliable delivery. By reducing order cycle time, businesses can enhance customer satisfaction and build loyalty, leading to repeat purchases and positive word-of-mouth. However, cost-conscious shoppers appreciate affordable or free shipping options to ensure the overall value of their purchases – so that’s something to be mindful of as a business.
Competitive Advantage: Swift delivery satisfies the need for instant gratification and meets consumer expectations in our fast-paced society, giving you a competitive edge in the market. Businesses that can deliver orders faster than their competitors have a higher chance of attracting and retaining customers.
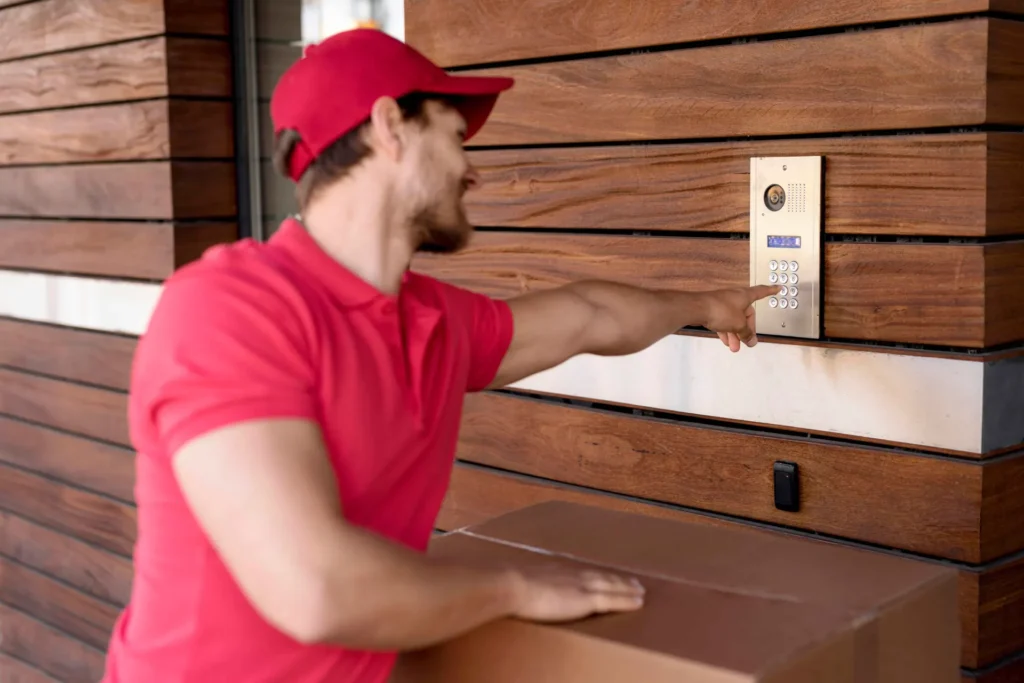
Strategies to Improve Order Cycle Time
There are several easily attainable strategies to employ in order to improve order cycle time:
Streamline Order Processing: Implementing efficient order management systems and automating order processing can significantly reduce cycle time. By eliminating manual errors and accelerating the order entry process, businesses can expedite fulfillment.
Optimize Inventory Management: Maintaining an accurate inventory and ensuring proper stock levels can prevent delays caused by stockouts or overstocks. Utilizing inventory management software can help optimize inventory levels and reduce fulfillment time.
Warehouse Layout and Organization: Designing a well-organized warehouse layout can minimize the time taken for order picking and packing. Employing strategies such as ABC analysis to prioritize fast-moving products and optimizing picking routes can streamline the process.
Warehouse Layout and Organization: Designing a well-organized warehouse layout can minimize the time taken for order picking and packing. Employing strategies such as ABC analysis to prioritize fast-moving products and optimizing picking routes can streamline the process.
Collaborate with Fulfillment Partners: For businesses that outsource their fulfillment, partnering with reliable and efficient third-party logistics providers can help improve order cycle time. Choosing partners strategically located near target markets can reduce transit time and expedite delivery.
Implement Advanced Technology: Leveraging technology such as barcode scanning, RFID tags, and warehouse management systems can enhance order accuracy, reduce errors, and speed up the overall fulfillment process.
What Buyers Value the Most in Order Fulfillment
By understanding the preferences and expectations of their target audience, businesses can provide a seamless and satisfying delivery experience that aligns with consumer needs and drives customer satisfaction.
An average customer expects the following:
Speed of Delivery: Customers value fast delivery. In a survey conducted by ShipBob, 82% of respondents said that same-day or next-day delivery options would make them more likely to purchase from an online store. By prioritizing quick delivery, businesses can meet customer expectations and gain a competitive advantage.
Transparency and Communication: Buyers appreciate clear and timely communication regarding their order status, including tracking information and estimated delivery dates. Implementing order tracking systems and sending proactive notifications can enhance customer satisfaction.
Order Accuracy: Accuracy is paramount in order fulfillment. Customers expect to receive the correct products in the right quantity and condition. Reducing picking, packing, and shipping errors is crucial to meeting this expectation.
Returns and Exchanges: An efficient returns and exchange process is essential for customer satisfaction. Simplifying the returns process, providing prepaid return labels, and offering hassle-free exchanges can create a positive customer experience.
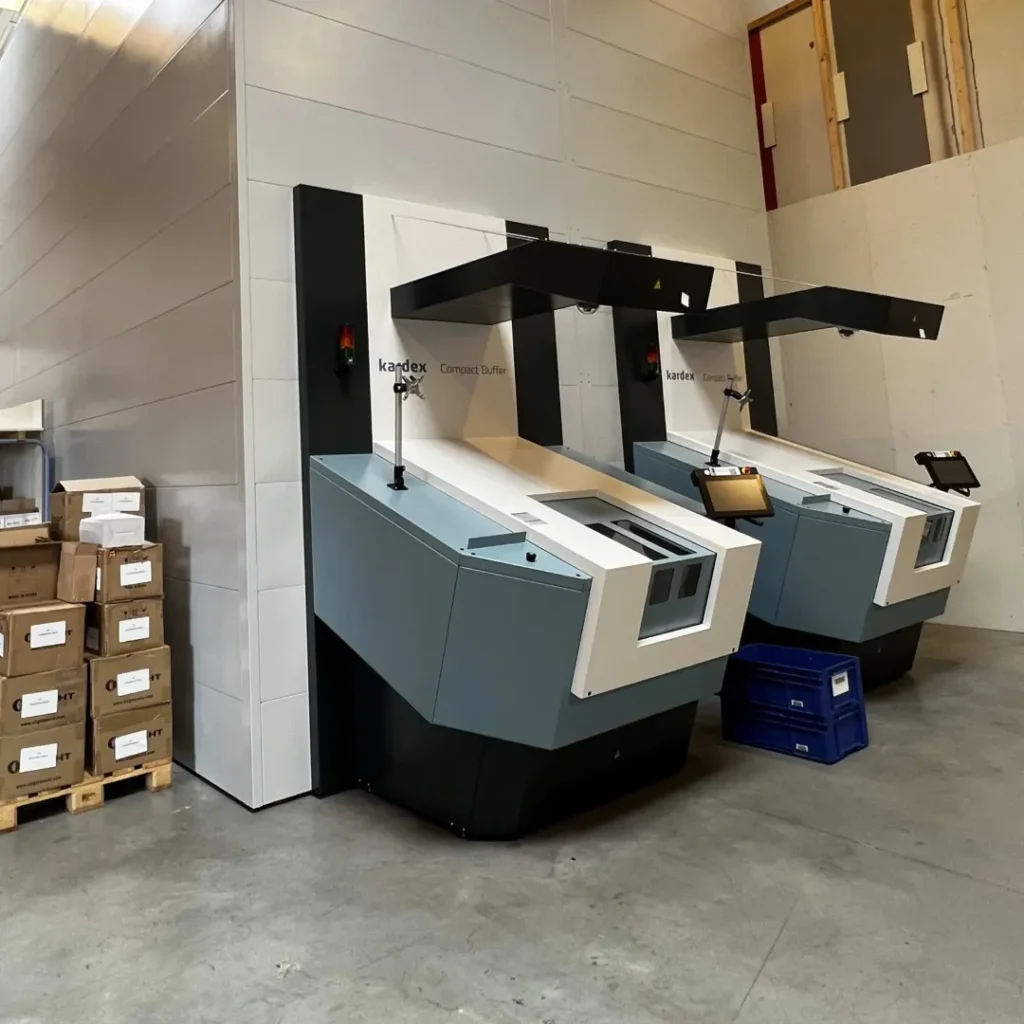
How Much Can You Save Using Warehouse Automation
Although the upfront investment in automation may seem daunting, it is essential to dispel common misconceptions surrounding its implementation to help warehouse operators decide whether the cost is justified.
The implementation of automation technology proves to be a cost-effective solution as labor expenses consume a significant portion, approximately 65%, of the warehouse operating budget. Implementing warehouse automation can potentially result in a significant reduction of operational costs by up to 30%. An additional cost-saving benefit is observed in the domain of inventory fulfillment, with the fulfillment accuracy rate currently standing strong at 63%.
By using automation tools, one can effectively minimize picking errors and enhance operational efficiency.